国家制造强国建设战略咨询委员会表示,新材料领域产业前景良好,到“十三五”末市场规模将达万亿之巨。
而据公开资料报道,工信部对全国30多家大型企业130多种关键基础材料调研结果显示:国内32%的关键材料仍为空白,52%依旧依赖进口,关键材料的国产化已经刻不容缓。
基于此,新材料在线®梳理出部分亟需进口替代的关键材料,并对其目前的国内外发展情况,以及国产化的主要难点进行简要分析。
如有疏漏不足之处,欢迎与小编联系指正。
半导体材料
半导体作为信息技术的核心,是一个回报慢,产业链长,资本、技术和专利壁垒高的产业。生产半导体芯片需要19种必须的材料,缺一不可,且大多数材料具备极高的技术壁垒。
中国是全球最大的半导体消费市场,半导体需求量全球占比由2000年的7%攀升至2016年的42%。然而我国半导体产业发展与其庞大的市场需求并不匹配,许多材料仍然依赖进口。
电子级多晶硅是纯度最高的多晶硅材料,纯度要求达到99.999999999%,也是半导体集成电路的关键基础材料。
图片来源:Slide Player
过去中国市场上的半导体用多晶硅材料完全依赖进口,世界范围内能生产电子级多晶硅的仅有Wacker、hemlock等企业,关键技术主要由德国、日本和美国的企业掌握。
2018年6月,江苏鑫华半导体研发团队在历经了317次电子级多晶硅生产试验,对629项技术、设备优化改进,以70%的国产设备,系统性解决了杂质释放问题,终于实现了国产电子级多晶硅的量产,目前年产能0.5万吨。
然而仅2017年,我国多晶硅进口数量达14.4万吨。虽然鑫华半导体的量产在一定程度上能缓解巨头垄断,但国内高品质电子级多晶硅缺口仍然十分巨大。
2、硅片
硅片也称硅晶圆,其主要作用是可以加工制作成各类电路结构,使之成为具有特定电性能的半导体产品,2017年市场规模达 86.8 亿美元。
图片来源:WaferPro官网
硅片的直径越大,其所能刻制的集成电路就越多,芯片的成本也随之降低。目前常用的硅片有6英寸、8英寸和12英寸,未来则将朝着18英寸发展。
但大尺寸硅片对技术的要求很高,主要原因在于:1 在大尺寸硅片的拉晶过程,晶柱的慢速旋转难以稳定,容易导致晶格结构缺陷;2晶柱的直径越大也意味着其重量越大,边缘处容易出现翘曲。这两个因素导致大尺寸硅片的良品率极低,进入壁垒极高。
因此,在全球的硅片市场中,日本信越、日本盛高的市占率为51%;但在大尺寸硅片领域(8英寸和12英寸),二者的市占率则提升至70%以上,形成寡头垄断。
据报道,国内目前8英寸硅片产能约为23.3万片/月,而需求量达到80万片/月; 12英寸硅片目前仅有上海新昇半导体实现了量产,但受限于产能,目前的需求仍旧大量依赖于进口。
目前国内虽有一些企业已经聚焦大硅片的生产,但产品的认证和产能的释放还需要一定的时间。如果没有关键技术、核心原物料的支持,未来会有一波大量的无效产能问题涌现。
光刻胶是一种耐蚀刻材料,主要应用于微电子领域的精细线路图形加工,是微制造领域最为关键的材料之一。
在光刻胶生产种类上,我国光刻胶厂商主要生产PCB光刻胶,而技术要求较高的显示光刻胶和半导体光刻胶生产规模较小,市占率极低;高分辨率的KrF(248nm)和ArF(193nm) 是技术壁垒极高的光刻胶材料,国内几乎全部依赖于进口。
放眼国际市场,该领域主要被日本合成橡胶、东京应化、住友化学、陶氏杜邦、德国巴斯夫等化工巨头垄断。
光刻胶的研发,难点在于其成分复杂、工艺技术难以掌握。关键生产原料如光引发剂、光增感剂等被外资垄断,开发所涉及的技术难题众多,导致高端光刻胶自给能力严重不足。
4、光罩
光罩是半导体核心工艺——光刻的关键器件,2017年市场营收为37.5亿美元。它是由石英玻璃作为衬底,并在上面镀上一层金属铬和感光胶的一种感光材料。它的主要作用是将半导体回路图,通过光刻制版工艺,将微米或纳米级的精细图案制成掩模版。
图片来源:Nikon官网
全球光罩产业生态分为半导体厂附属的光罩部门,以及独立型光罩供应商两大类。两者比重约为65% 和 35%,半导体大厂英特尔、台积电、三星、中芯国际内部都有附属的光罩部门,而独立型的光罩供应商主要有日本凸板Toppan 、大日本印刷DNP 、美国Photronics Inc等,三者的合计市场份额超过80%。
国内也有光罩供应商,但多数都停留在提供八英寸晶圆和低端工艺技术上。原因在于,光罩产业的机械设备投入十分庞大,且主要的高端技术还掌握在外商手中。
5、CMP抛光材料
CMP(Chemical Mechanical Polishing),即化学机械抛光,是集成电路制造过程中实现晶圆全局均匀平坦化的关键工艺。
图片来源:AGC官网
抛光材料是CMP工艺过程中必不可少的耗材。根据功能的不同,可划分为抛光垫、抛光液、调节器、以及清洁剂等,其中主要以抛光液和抛光垫为主。
CMP抛光材料具有技术壁垒高,客户认证时间长的特点,全球市场一直以来处于寡头垄断的格局。抛光液的市场主要由日韩和美国公司所垄断,占据全球90%以上的市场份额;抛光垫是市场主要被陶氏化学公司所垄断,市场份额超过80%。
国内企业的抛光液生产以中低端产品为主,仅能用于金属、手机玻璃盖板等领域的抛光。上海安集微电子于2007年正式上线半导体用抛光液,率先打破高品质抛光液的国外垄断,但还受限于产能。
2017年12月,鼎龙股份公告称其第一款抛光垫产品通过了客户验证,并进入该客户供应商体系。这意味着中国自主研发的半导体抛光垫材料首次进入商业市场,中国也成为继美国和日本之后第三个抛光垫商业化生产的国家。
抛光垫的技术壁垒在于沟槽设计,合理的沟槽设计可以改善抛光液的流动并带走切削的细屑,使晶圆表面最终能形成完美的镜面效果;
抛光液的技术壁垒在于调整抛光液的组成以改善抛光效果,其配方则是影响抛光效果的决定性因素。
6、湿电子化学品
湿电子化学品是在微电子、光电子湿法工艺制程中使用的各种电子化工材料。其品种类繁多,主要应用于面板、半导体及太阳能电池三大领域。
当前世界湿电子化学品的市场格局主要可分为三大块:欧美传统化工企业的市场份额约为35%;日本约十家湿电子化学品企业的市场份额约为28%;中国和韩国的市场份额约为35%。
目前,国内湿电子化学品的研发水平,大部分集中在G2水平,在中低端市场的应用势头良好。
随着国家02专项的大力支持和优秀企业的自主研发,江化微等本土企业的纯化工艺技术取得突破,部分领域的产品已经达到G3标准,有望进一步打开国内的高端应用领域市场。
溅射靶材是制备电子薄膜的关键材料,主要应用于半导体芯片、液晶显示器、太阳能电池等领域,其中半导体芯片对溅射靶材的金属纯度要求最高。
图片来源:德国亥姆霍兹联合会官网
超高纯金属溅射靶材在半导体芯片制造领域,美国和日本的少数公司,占据了 80%以上的市场份额。
近年来部分国内企业如江丰电子、晶联光电等企业在高纯溅射靶材生产技术及市场方面均取得了关键突破,部分产品已打入核心客户主流供应链中,并批量供货。
由于高纯溅射靶材的认证时间长达2-3年,想要实现产品大规模的国产化还需要一定的时间。
半导体封装是指将晶圆按照产品型号及功能需求加工得到独立芯片的过程。目前的封装材料主要采用环氧模塑料(EMC),占比在97%左右,EMC中70%-90%的成分为硅微粉。据CNCET估算,2017年全球EMC市场约23.9亿美元。
图片来源:nichetech官网
EMC的生产关键在于配方,针对不同的细分用途使用不同的配方。日本企业以其产品在操作性和可靠性上的技术优势而在中高端市场占据着较大市场份额,而欧美系、韩系和国内企业则以成本优势占据相对低端的市场。
2017年我国EMC年产能达14.3万吨,行业龙头企业如衡所华威已经能够参与国际市场竞争,现有生产线13条,涉及一百多个品种,市场占有率国内第一、全球第五。
近年来以华飞电子为代表的国内企业突破国外技术封锁,掌握高纯小粒度球形硅微粉的生产技术,其产品占据国内70%的份额,并和国外两家龙头企业共同瓜分50%的国际份额。
国产EMC和硅微粉具有本土化优势,完全可以替代进口,未来市场前景非常广阔。
显示材料
2017年国内面板产能超过韩国位列全球第一,占了全球市场超过22%的份额,产业规模超过3000亿元。根据IHS预计,未来五年,全球平板显示市场中大尺寸超高清面板年复合增长率将超过25%。
虽然我国面板产业规模大,但基本属于加工组装型,不但生产线要从国外进口,而且制造面板的关键材料中有约70%也都严重依赖进口,国有化率很低,进口替代需求紧迫。
平板显示玻璃基板是平板显示产业的核心材料,其质量关系到显示面板成品的分辨率、透光度、厚度、重量、可视角度等指标,约占整个显示面板产品成本的20%。
图片来源:Corning官网
发达国家在平板显示玻璃基板制造领域处于垄断地位,全球TFT-LCD用玻璃基板市场份额,90%以上集中在美国康宁、日本旭硝子、电气硝子、安瀚视特等几大厂商。
大尺寸化、轻薄化液晶面板是今后基板玻璃市场的需求重点。彩虹集团、东旭集团、中国建材国际工程集团等本土企业大力推进玻璃基板国产化,目前已经取得突破性进展,中小尺寸面板市场份额已达80%。
但国内目前玻璃基板产品的供应缺口依然高达一半左右,尤其是G8.5+、G6LTPS高精细玻璃基板等产品,几乎100%依赖于进口。
微球是一种现代工业基础材料,应用于多个领域。
目前液晶显示屏里的微球基本上全被日本垄断了,生物制药的微球基本上被美国GE公司垄断。仅微电子领域,国内每年就要进口价值约几百亿元人民币的微球。
微球附加值高,制备技术要求苛刻,如粒径精确性、粒径分布、机械强度、表面性能、洁净度控制等。
3、偏光片
偏光片是一种复合材料,可实现液晶显示高亮度、高对比度的特性,是液晶面板的三大关键原材料之一,占其成本的10%左右。LCD模组中需要两张偏光片,分别位于玻璃基板两侧,缺少任何一张偏光片都无法显示画面。
图片来源:LG化学官网
偏光片行业具备较高的技术,人才,资金和客户认证壁垒,市场集中度较高。韩国LG化学,日本日东电工和住友化学三足鼎立,占据全球 65%的市场份额,前五大厂商占据全球84%的市场份额。
根据有关数据显示,2017年国内偏光膜市场规模为30.4亿美元,同比快速增长13.4%,占全球市场份额29.9%。预计到2020年,国内偏光片市场规模可达53.2亿美元,占全球市场份额提高至40.2%。(数据尽量用图表)但目前国产偏光片占国内需求比例不足40%,仍需大量进口。
关键材料依赖进口,阻碍偏光片国产化进程。偏光片的上游核心原材料PVA和TAC膜目前仍然主要依赖日韩供应商,。
4、液晶材料
液晶材料是液晶面板的关键基础材料。
任何液晶单体都只具有一方面或几方面的优良性能,因此通常选用多种液晶单体,调制成综合性能优异的混合液晶,以满足显示用液晶材料的各项性能要求。
图片来源:群创光电官网
液晶材料的制备对原料纯度和生产工艺要求严格,目前全球高端液晶材料的供应商主要以三大厂商为主,德国MERCK、日本CHISSO、日本DIC,三家企业构建了严密的专利网,占据了全球大约95%的市场份额,长期垄断该高端产品市场。
目前,国内生产液晶材料的企业多数以生产中间体、单体为主,且以TN、HTN、STN型系列的中低端液晶材料为主,TFT混合液晶则主要依赖进口。
国内企业生产的液晶中间体和单体液晶,出口给国外厂商合成TFT混合液晶产品。由于中间体化合物到成品液晶材料技术难度大,外企获取了超过67%的垄断利润。
图片来源:显华化工官网
5、OLED发光材料
OLED发光材料是OLED显示面板配套的关键材料,其在OLED中的面板成本占比约为12%,是OLED产业链中技术壁垒最高的领域,市场竞争小、毛利率高。
目前全球OLED发光材料的供应权基本掌握在海外厂商手中。绿光材料的主要供应商为三星SDI、默克公司;红光材料的主要供应商为陶氏化学;蓝光材料主要由出光兴产供应。
国内OLED有机材料产品主要是技术含量低的中间体和单体粗品,高纯度升华品较少。
究其原因,主要是国内企业在终端材料上的研发起步较晚,缺乏关键的材料专利,限制了单体材料向终端材料制造工艺的发展。
航空材料
航空材料泛指用于制造航空飞行器的材料,其中机体材料和发动机材料是重要的结构材料。
据《2025年航空技术发展预测报告》中指出,在43项航空技术中,航空材料重要性位居第二,“一代材料,一代飞机” 成了世界航空发展史的一个真实写照。
我国目前的航空材料现状与新一代航空产品对材料的需求之间尚存在较大的差距,成为制约我国航空产业发展的重要因素。
1、高温合金
高温合金是指以铁、镍、钴为基,能在600°C以上的高温及一定应力作用下长期工作的一类金属材料,是制造航空发动机热端部件的关键材料。
在世界先进航空发动机研制中,高温合金用量已占到发动机总量的40%-60%。
图片来源:HuffPost官网
目前,高温合金主要应用于航空发动机的四大热端部件:燃料室,导向器,涡轮叶片和涡轮盘。此外,还用于机匣,环件和尾喷口等部件。由于航空发动机结构较为复杂,各部位温度和受力情况等,差别较大,因此对材料的要求和选用就各不相同。
经过多年的发展,我国的高温合金产业在研发和生产上都形成了一定的规模和水平,但与发达国家相比还存着一些差距,主要产品还是集中在中低端的应用上。
我国高温合金总产能约为1.26万吨,实际产量约0.8-0.9吨。根据测算,国内高温合金需求约为3.93万吨,年市场缺口2万余吨,特别是航空航天等高端领域的应用主要依赖于进口,进口替代需求紧迫。
目前,全球每年消费高温合金材料近28万吨,市场规模达100亿美元。全球范围内能够生产航空航天用高温合金的企业不超过50家,主要集中在美国、俄罗斯、英国、法国、德国、日本和中国。
随着我国科技实力的发展,以钢研高纳为代表的一部分企业,已经在科研创新和生产工艺上取得了突破,部分产品可以替代进口,可以预期整个行业也会向着高端化的方向发展。
铝锂合金中锂既能降低铝的密度又能提高弹性模量,向铝金属中每添加1%的锂,铝合金的密度就下降约3%,而其弹性模量则会上升约6%。
铝锂合金的成本大约只是碳纤维增强塑料的10%,从而成为碳纤维增强塑料强有力的竞争产品,是航空航天材料中发展最为迅速的一种先进轻量化结构材料。国产大型客机C919就大范围采用了铝锂合金。
图片来源:aeronauticapy.com
据统计,美国铝业公司是全球铝锂合金产能、产量最大的生产企业,约占全球份额的55%;俄罗斯铝业联合公司约占25%,其他企业合计约占20%。
国内的西南铝业也能生产铝锂合金,不过还未形成大规模量产的能力,远远不能满足国产大飞机的需求。江苏豪然采用的是喷射成形制造铝锂合金,但目前还未进行规模化生产。
未来,独立开发和研制新型高强、高损伤容限铝锂合金是我国铝锂合金发展的重要方向。
每架大飞机的起落架用特种高强度钢约有15吨,目前美国九成以上飞机起落架材料由美国国际镍公司研发的300M钢担纲,其强度在1900-2100MPa,相当于20000个大气压。
世界高品质不锈钢生产国主要集中在西欧、美国、日本等,其年产量约占世界总产量的75%。其中,瑞典的高品质不锈钢在世界不锈钢产量中的比例最高。
在钢铁行业,5个PPM的顶级钢是高端轴承所需要的。高端轴承用钢的研发、制造与销售基本上被世界轴承巨头美国铁姆肯、瑞典SKF所垄断。
目前,我国的高端合金钢材研制水准与欧洲、俄罗斯相比基本相当或略有优势,但在材料创新基础研究能力,尤其是高纯度熔炼技术方面与美国还有较大差距,存在很大提升空间。
此外,在新一代数字化和智能化控轧控冷技术、先进热处理技术、变截面轧制技术、温度梯度轧制技术、高精度轧制技术方面,我们与美国、日本还有不小的差距,有的还停留在实验室阶段。
碳纤维是指由碳元素组成的纤维,标准弹性率碳纤维的碳素含量在90%以上,高弹性率碳纤维就几乎是由100%的碳素组成,主要特点是质量轻且强度高,高端应用集中在飞机的机身、主翼、尾翼等部位。
图片来源:Composites Manufacturing Magazine
目前我国碳纤维的‘卡脖子’问题主要在下游应用环节,即复合材料和制品方面。
碳纤维复合材料中的关键复合辅材是环氧树脂,它的附着力很强,能将碳纤维粘接在一起。但目前国内生产的高端碳纤维,所使用的环氧树脂全部依赖于进口。
2018年中复神鹰T1000级碳纤维工程化取得突破性进展,其百吨级T1000碳纤维生产线实现投产且运行平稳,但受限于产能原因高端材料仍然依赖进口。
现在国际碳纤维材料市场,小丝束碳纤维技术目前被日本东丽、帝人东邦和三菱化学等企业控制,市场占有率70%;大丝束碳纤维由美国卓尔泰克(2013年已被日本东丽收购)、德国西格里、福塔菲尔、阿尔迪拉控制,市场占有率80%左右。
碳纤维及其复合材料对支撑我国制造业转型升级、保障国防安全等具有重要作用,因此提高国产碳纤维的研发和大批量稳定生产能力迫在眉睫。
聚酰亚胺是指主链上含有酰亚胺环(-CO-NH-CO-)的一类聚合物,是综合性能最佳的有机高分子材料之一,其耐高温达400℃以上,长期使用温度范围为-200-300℃,无明显熔点,绝缘性能佳,应用前景广阔。
聚酰亚胺材料在航空航天、军事、高端电子等敏感领域有着难以替代的作用,国外的大多数聚酰亚胺原材料、技术和产品对我国实行了严格的封锁。
德国、英国、法国,美国,日本,韩国等掌握着核心科技。国内目前仅在中低端聚酰亚胺薄膜及聚酰亚胺纤维等少数领域实现了量产,但还存在生产规模小、产品较为单一、产品精细化程度不够等问题。
据相关报告显示,2017年国内聚酰亚胺的进口量为2846吨,进口依赖度达到了41.6%。
对位芳纶是一种综合性能优异的纤维丝,具有高强、高模、阻燃等性能,是航空航天、信息技术、国防和汽车工业等领域重要的基础材料,具有广阔的市场前景。
自20世纪70年代美国杜邦成功进行对位芳纶产业化之后,主要生产技术始终掌握在美日等国际巨头手中,被视作一种战略性物资材料,对中国实行禁运禁售。
2011年5月,泰和新材率先发布公告宣布实现对位芳纶的产业化生产,完成了从实验室到商业化生产的飞跃,进入国内市场。
泰和新材和中蓝晨光已经掌握千吨级对位芳纶生产技术,国产化进程中的问题和机遇并存。
当下,国内对位芳纶的市场局面是国产率不足。据相关数据统计,2017年国产对位芳纶消耗量在9000吨左右,国产供给占比仅占10%-15%,其余全部来自进口。
未来,国内对位芳纶生产企业应该推进对位芳纶产品集群建设,突出链条化、多元化、规模化发展,提升产品集群综合竞争力,尽早实现大规模的进口替代。
新能源电池
1、锂离子电池隔膜
锂离子电池隔膜的主要作用是使电池的正、负极分隔开来,防止两极接触而短路,此外还具有能使电解质离子通过的功能,是电池的四大核心材料之一。
图片来源:Science Direct
目前,全球锂离子电池隔膜材料的市场份额主要由日韩企业掌握。旭化成、东丽和SKI三家企业占据了全球超过50%的市场份额。
国内隔膜行业结构性产能过剩,市场上出现两极分化的局面。一方面,供应于3C类电池市场的中低端产品产能明显过剩,产能利用率在50%左右。另一方面,高端动力电池隔膜供不应求,其中高端湿法隔膜进口比例超过90%。
锂离子电池隔膜制备的技术难点在于造孔的工程技术和制造设备。
国产隔膜普遍存在的问题是一致性有待提高,主要体现在不规律的缺陷、厚度、孔隙率、孔隙分布以及孔径分布等方面。
以上为小编梳理的20种亟需进口替代的关键材料。材料作为先进制造业等新兴产业的基石,其研发和产业进程将成为我国实现制造业强国的关键支撑。
那么,进口替代浪潮下,新材料企业都有哪些的机遇与挑战?
欢迎您参加2018中国新材料资本技术秋季峰会,与1000+新材料产业相关政府领导、院士专家、园区代表、知名新材料企业家、知名投资人等行业菁英,共同探讨!
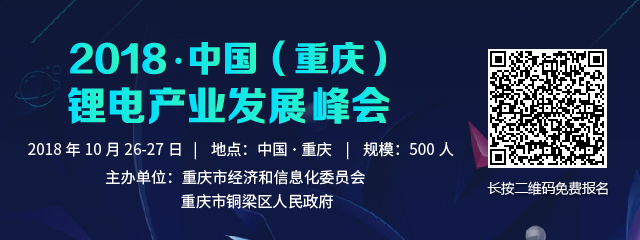